
If the demand is lower or fluctuates often, stocking at distribution centers may be required to better meet service levels. If the demand is higher, a direct to store distribution strategy may be more appropriate. In planned cross-docking specific product is chosen with like characteristics such as those with consistent demand that maintain a stabilized flow based on sales history, averages and speed of movement.

Variations of cross-docking methods can be leveraged to yield different advantages. Inventory management becomes more efficient as the inventory moves directly from the receiving to the shipping docks eliminating the need to store the materials thus reducing the total system inventory in the supply chain process. Warehouse operations become more efficient through the cross-docking process since the material does not have to be stored at the warehouse and moves directly from the receiving docks to the shipping docks or staging areas. This eliminates the need to stock at the warehouse saving resources at the warehouse like labor, space, equipment and technology resources by simplifying the process. This is usually done to sort material intended for different destinations or to combine material from different origins that are going to a similar destination.
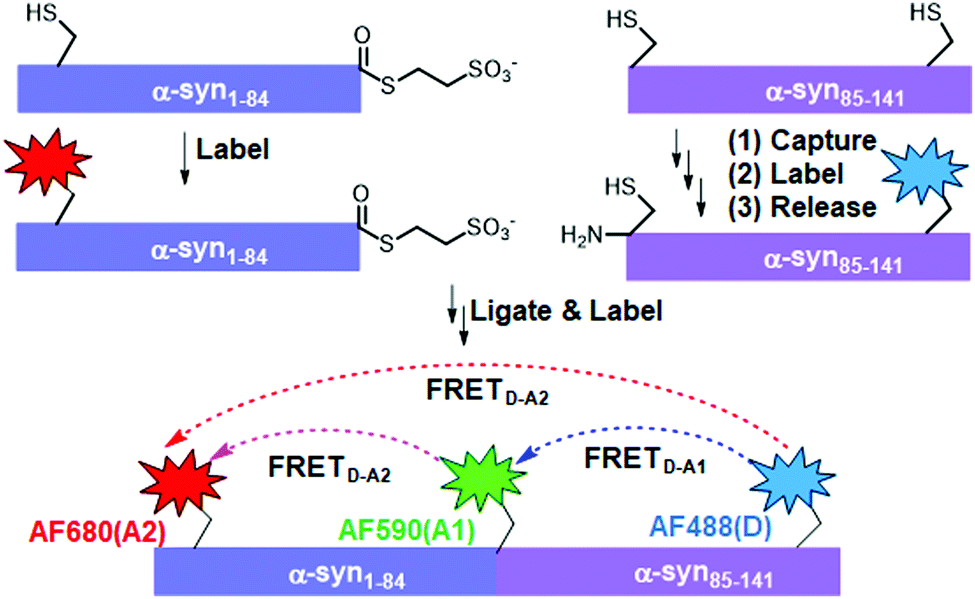
This is the process of unloading materials from an incoming method of transportation and loading them directly into an outbound one requiring little or no storage in between. Cross-docking is a practice that takes place at a distribution center. Supply chain management is all about the flow of materials.
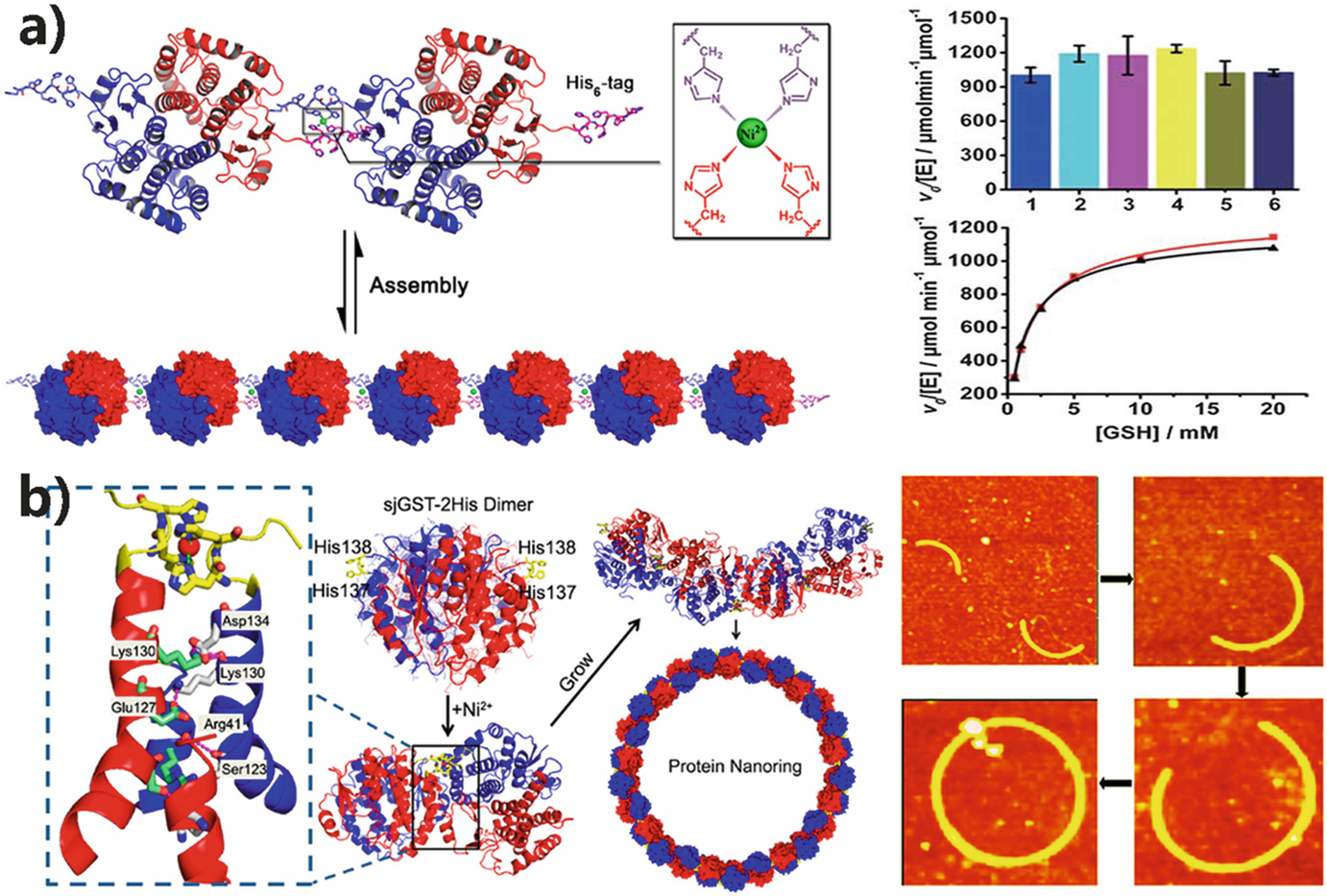
What Is Cross-Docking? How Does Cross-Docking Work?
